Understanding Glycol in Process Cooling and HVAC Systems: Essential Knowledge and Best Practices
- Jill Nelson
- Mar 10
- 4 min read
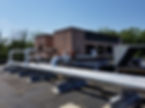
What is Glycol?
Glycol is a type of chemical compound characterized by having two hydroxyl (OH) groups attached to different carbon atoms. The most common types used in HVAC and industrial applications are:
Ethylene glycol (C2H6O2): A viscous liquid with a sweet odor and typically colored for identification purposes. It has excellent heat transfer properties and is commonly used as an antifreeze but is toxic if ingested.
Propylene glycol (C3H8O2): A less toxic alternative to ethylene glycol with similar properties. It's considered safer for applications where there might be human contact or environmental concerns. "Food-grade" propylene glycol refers to a high-purity version that meets FDA requirements for incidental food contact, making it the preferred choice in applications where safety is paramount.
In HVAC and process cooling systems, glycol is typically mixed with water to create a solution that:
Lowers the freezing point of water (preventing pipe bursts in cold conditions)
Raises the boiling point (allowing for higher temperature operation)
Provides corrosion inhibition when properly formulated with additives
Maintains effective heat transfer properties
The concentration of glycol in the water mixture determines the freezing point protection, with higher concentrations providing protection at lower temperatures.
Historical Development
Glycol has played a significant role in HVAC and process cooling, particularly as a heat transfer fluid. Its use dates back to the early 20th century, when the need for efficient heating and cooling systems became more pronounced in industrial and commercial applications. Initially, both ethylene glycol and propylene glycol were popular choices for antifreeze solutions.
Over the past 40 years, propylene glycol has emerged as the safer and more environmentally friendly option. Most design engineers now specify food-grade propylene glycol (like Dow Frost or equivalent) due to its reduced toxicity and safer handling characteristics.
Glycol formulations have been refined over time with various additives to address specific performance needs. These additives typically include corrosion inhibitors, pH buffers, and anti-foaming agents that help maintain system integrity and efficiency. Different manufacturers offer proprietary blends designed for specific applications and operating conditions, allowing for for tailored solutions based on specific system requirements.
Common Applications
Glycol is commonly used in:
Chilled water systems
Hot water systems
Heat recovery loops
Thermal energy storage
Â
Its ability to lower water's freeze point allows HVAC and process cooling systems to operate efficiently in various climates, significantly reducing the risk of freezing.
Design Considerations
HVAC and process cooling design engineers must account for several factors when working with glycol systems:
Temperature Range: Consider both freeze point and boiling point temperature ranges for system operation.
Material Compatibility: Ensure long-term compatibility with pumps, piping, and heat exchangers.
Viscosity Management: Account for glycol's increased viscosity (measured in cP or centipoise), particularly in pump selection. This is especially important at lower temperatures where viscosity increases significantly.
Heat Transfer Optimization: Design for appropriate flow rates to optimize heat transfer, especially in heat exchangers.
Piping Configuration: Minimize pressure drops, avoid dead spots where glycol can stagnate, and ensure proper insulation R-value to reduce heat loss.
Emergency Planning: Consider emergency power for circulating pumps or incorporate freeze protection pumps where applicable.
Installation and Commissioning
Chilled water and hot water systems typically undergo several important steps during installation and commissioning:
1.     Pressure test chilled water and hot water systems
2.     Clean systems with solutions like trisodium phosphate (TSP)
3.     Add glycol with rust inhibitor mixed to a specific freeze protection point
4.     Circulate for a designated period
5.     Verify the specified freeze point using a digital refractometer
Maintenance Requirements
All glycol systems require specific preventive maintenance (PM):
Concentration Monitoring: Glycol concentrations typically decrease over time to levels that provide inadequate freeze protection. While the primary cause is often maintenance activities where portions of the system are drained and refilled with water only (without adjusting the makeup system's glycol-water mixture), some glycol can also be lost through small leaks, venting, or chemical breakdown over extended periods. If the glycol concentration becomes too diluted, the system loses its freeze protection capabilities, putting pipes and equipment at risk during cold conditions.
Regular Testing: Regular testing of glycol freeze protection points is essential for system reliability. Using digital refractometers or other appropriate testing equipment, maintenance personnel should verify that the glycol solution maintains the proper freeze point specified in the system design. Seasonal testing is particularly important, especially before cold weather periods. Besides freeze protection, regular testing can also reveal issues with pH levels and inhibitor concentrations that could lead to corrosion within the system. Establishing a consistent testing schedule as part of the preventive maintenance program helps prevent system damage and extends equipment life.
Flow Verification: Proper flow rates are essential for optimal heat transfer in glycol systems. Regular verification using circuit balancing valves or an ultrasonic flow meter ensures the system is operating at design specifications. Inadequate flow can lead to poor heat transfer, while excessive flow can cause erosion and unnecessary pump energy consumption. Periodic flow testing also helps identify potential blockages, air entrapment, or pump performance issues before they develop into larger problems.
Performance Checks: Thermal imaging provides valuable insights into the performance of heat exchange equipment. By scanning coils, heat exchangers, and piping systems, maintenance personnel can identify uneven heat distribution, blocked passages, air pockets, or fouling that might not be apparent through other testing methods. These proactive inspections can identify inefficiencies before they impact overall system performance, helping maintain optimal energy efficiency and extending equipment life.
MSC Professional Services
With decades of specialized experience in industrial, institutional, and commercial facilities, MSC has the technical knowledge and practical expertise to ensure your glycol systems operate reliably, efficiently, and safely throughout their service life.
Our comprehensive glycol system services include:
Preventive Maintenance Programs: Development and implementation of detailed PM plans specifically designed for glycol systems, including regular concentration testing, corrosion monitoring, and system-wide performance verification.
System Assessment: Detailed inspections of existing glycol systems to verify compliance with original design intent and identify opportunities for improved performance and efficiency.
Emergency Response: Rapid response services for glycol system issues, including freeze protection emergencies, leaks, or performance problems.
Technical Consultation: Expert advice on glycol selection, system conversion, and optimization from our experienced team of mechanical engineers and HVAC and process cooling specialists.
Custom Solutions: Design-build services for new installations or system upgrades, tailored to your specific facility requirements, with particular attention to glycol selection, concentration, and distribution system design.
Facility Staff Training: Customized training programs to help your maintenance team understand proper glycol system management, testing protocols, and early problem identification.