Physics at Play: Solving the Mystery of Recurring VFD and Motor Failures
- MSC
- Sep 29, 2023
- 2 min read
As commercial/industrial HVAC service specialists, we at MSC often deal with complex challenges requiring extensive testing and diagnostics. But sometimes, perplexing problems turn out to have simple solutions.
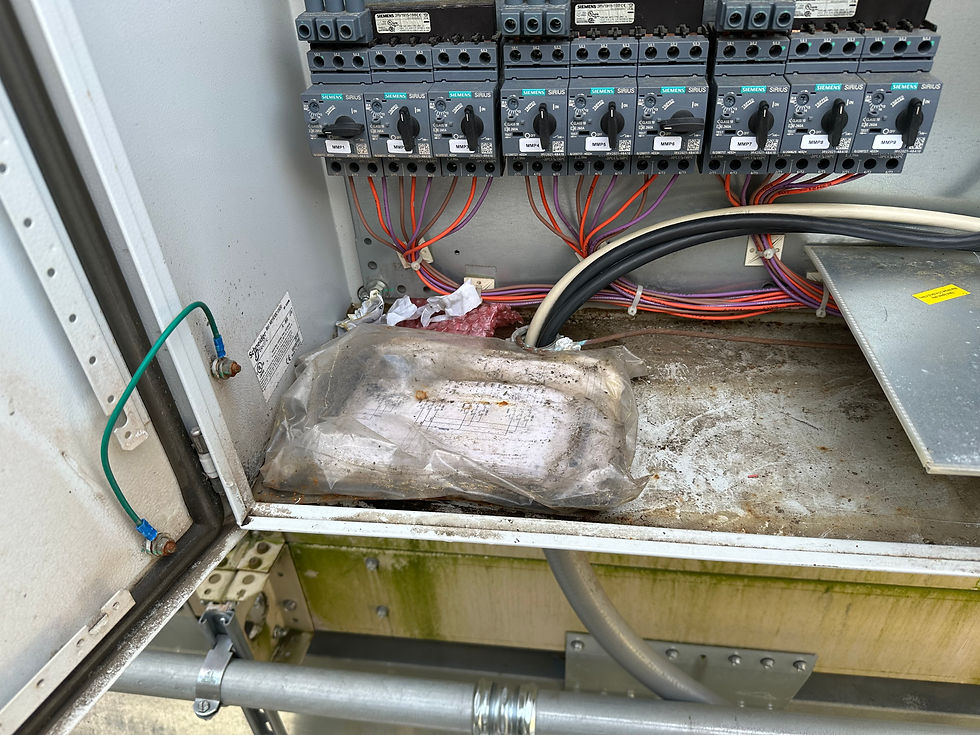
MSC recently received a call from a large corporate office building. Variable frequency drives (VFDs) and fan array motors serving their 60-ton rooftop split air handling unit were failing at an alarming rate. Over six months, another HVAC contractor had to replace three VFDs and four 10hp motors and responded to numerous service calls for other recurring issues. The contractor had been unable to pinpoint the reason behind these frequent failures in such a short period.
The situation was becoming financially unsustainable, and the building operators, desperate for answers as to why the equipment kept failing, called MSC and described what was happening. It was a genuine head-scratcher, so we asked the customer to provide additional information, including service reports, email correspondence, and equipment photographs. One of the photos showed a puddle of water inside the bottom of a VFD/control cabinet. After reviewing the materials, we had a strong hunch about the root cause. A service technician was dispatched to the site to investigate our suspicions.
The technician climbed to the roof and went to the air handler, where he observed a large VFD panel for the fan array enclosed in a cabinet mounted on the exterior. The cabinet was equipped with an air intake and an exhaust fan to remove heat. Our tech asked about the puddle in the bottom of the cabinet and was told by the maintenance supervisor that the water was sometimes as much as an inch in depth. The assumption had been that rainwater was coming in, so a maintenance team member had applied copious amounts of caulk to seal it. The real issue, however, was quite different.
What was happening was that during the day, cool air exiting the plenum from the discharge side of the air handler was infiltrating the hot, humid control cabinet through an electrical conduit that was never adequately sealed at installation. This caused condensation on the VFDs, fuses, terminal blocks, keypads, and other electrical controls.
At night, after the unit shut off and outdoor temperatures cooled down, the warm, moist air in the cabinet would migrate back through the unsealed conduit into the air handler, creating condensation inside the motors.
We sealed the conduit from the unit into the control cabinet using a high-grade silicone sealant with a tube insert. This sealant needed 24 hours to cure properly, so to minimize disruption, we performed the repair on a cooler Saturday when the unit could be safely turned off for at least a day. We then meticulously cleaned the VFD cabinet, inspected all terminations, assessed the drives and motor functionality, and ensured everything was completely dry.
The building owner was understandably happy with the resolution to their problem. However, they couldn't help but express their disappointment at the significant expenses they had incurred for what turned out to be a simple fix.
Comments