PROJECT BACKGROUND:
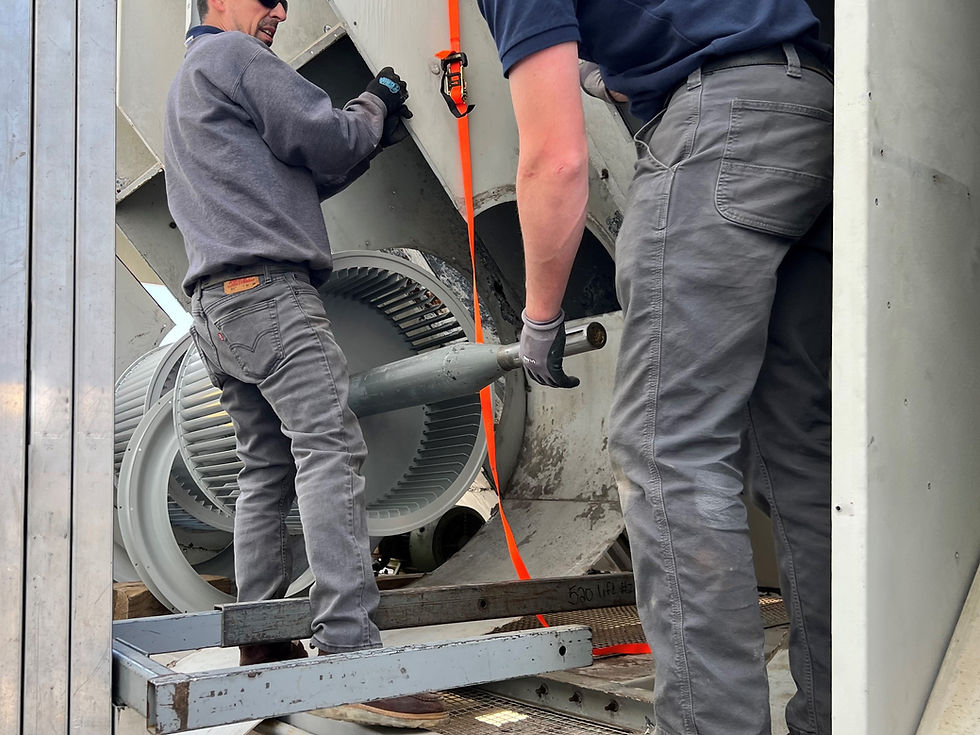
MSC recently undertook a significant project to revive a mothballed laboratory facility that had stood vacant and unattended for nearly five years. During this period, the four-story, multi-space 150,000 sq. ft. building received minimal attention, with rare sporadic checks only to ensure the heating system was still operational. Preventive maintenance had been almost nonexistent.
As expected, numerous building systems were found to be in disrepair, demanding intensive restoration. MSC was tasked with bringing the facility back online, with the owner’s stipulation that it be done as cost-effectively as possible, by repairing and replacing only what was necessary to restore functionality. We developed a detailed three-pronged approach after thoroughly assessing all equipment and systems.
THE APPROACH:
Utility and Equipment Restoration:
Implemented lockout/tagout and confined space safety protocols
Drained, flushed, and cleaned hydronic systems
Replaced air handler filters
Conducted comprehensive maintenance on air compressors
Thoroughly cleaned shell-and-tube heat exchangers
Replaced inoperable electrical components, including breakers, starters, and VFDs
Replaced bearings on several pumps and fans
Rebuilt two condenser water pumps and two essential AHU motors
Performed thorough cleaning and extensive repairs on severely damaged cooling towers, including reconstruction of leaking basins and epoxy recoating
Identification and Resolution of Heating and Cooling Issues:
Replaced six malfunctioning RH control valves, a chilled water control valve, DPT, and several temperature and pressure transmitters
Installed data loggers in strategic locations to continuously monitor system performance
Adjusted airflow based on data analysis and collaborated with third-party experts for laboratory hood and flow sensor repairs
Delved into BAS software to decipher system sequences and made necessary improvements due to the absence of operation
Planning for the Future:
Compiled a prioritized list of necessary repairs and replacements categorized as “very important,” “somewhat important,” and “nice to have” to assist the client in developing short-term and long-term budget plans
Secured a contract for future preventive maintenance, ensuring the facility’s sustained operational efficiency
Outcome:
MSC’s meticulous approach resulted in the successful revival of the facility. By systematically addressing utility issues, resolving heating and cooling challenges, and providing the client with a clear roadmap for future maintenance, the building was restored to its functional state and prepared for long-term sustainability. New tenants have seamlessly moved into the facility, confident in its operational efficiency. MSC has been entrusted with all future preventive maintenance, ensuring the facility's continued smooth and efficient operation.
Comments